Top 5 Forklift Training Mistakes to Avoid for Optimal Safety and Efficiency
- Mark Smith
- Aug 27, 2024
- 3 min read
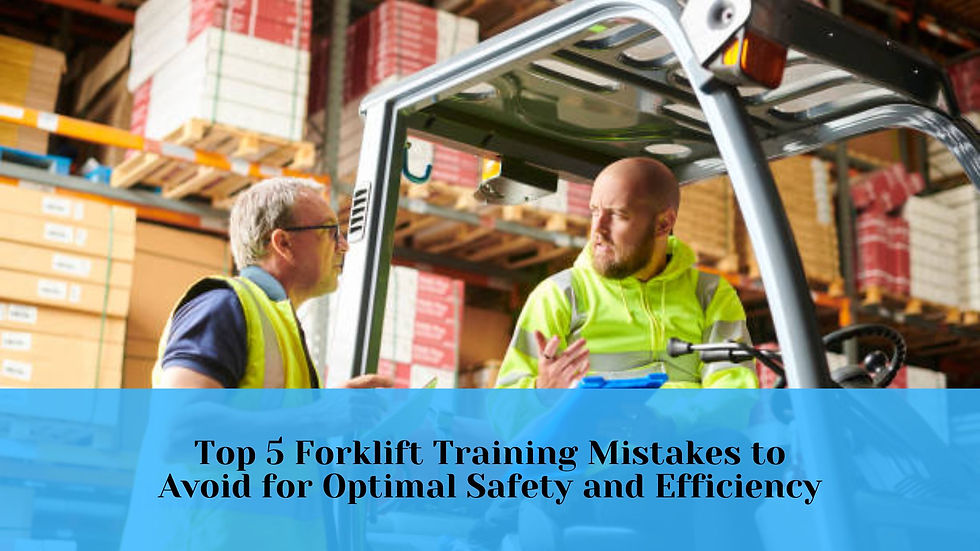
Forklifts are essential tools in many industries, from warehouses to construction sites. However, their effectiveness and safety hinge significantly on proper training. Ensuring that your team is well-trained in forklift operations not only boosts productivity but also prevents accidents and promotes a safer workplace. To help you maximise the benefits of forklift training, we’ve identified the top five mistakes to avoid for optimal safety and efficiency.
1. Neglecting Proper Training for New Operators
One of the most critical mistakes is failing to provide comprehensive training for new forklift operators. In many workplaces, employees might be quickly shown how to operate a forklift without a formal training programme, assuming that basic instructions are sufficient. This approach is risky and often leads to accidents.
Why It Matters: Forklift operation requires specific skills and knowledge, including understanding load capacities, vehicle stability, and navigating tight spaces. Without thorough training, operators may misjudge these factors, leading to potential safety hazards and operational inefficiencies.
What to Do: Ensure that all new operators undergo a structured training programme that covers all aspects of forklift operation, including safety protocols, equipment maintenance, and handling procedures. Investing in a recognised training course not only equips operators with essential skills but also complies with legal requirements.
2. Skipping Regular Refresher Courses
Another common mistake is overlooking the need for regular refresher courses. While initial training is crucial, skills and knowledge can deteriorate over time. Regular updates and refresher courses are necessary to keep operators informed about new safety regulations, technological advancements, and best practices.
Why It Matters: Forklift technology and safety regulations evolve, and operators need to stay updated to handle modern equipment and comply with the latest standards. Skipping refresher courses can lead to outdated practices and increased risk of accidents.
What to Do: Schedule periodic refresher courses for all forklift operators. These sessions should review safety procedures, operational updates, and any changes in regulations. Regular training helps reinforce best practices and keeps safety at the forefront of operations.
3. Overlooking the Importance of Practical Training
Many training programmes focus heavily on theoretical knowledge, sometimes at the expense of practical, hands-on experience. While understanding forklift mechanics and safety rules is essential, practical training ensures that operators can apply their knowledge effectively in real-world scenarios.
Why It Matters: Theoretical knowledge alone doesn’t prepare operators for the practical challenges they’ll face on the job. Hands-on training helps them develop muscle memory and the ability to handle various operational situations confidently.
What to Do: Integrate ample practical training into your forklift training programme. Operators should spend significant time practising in controlled environments, learning how to manoeuvre the forklift, handle loads safely, and respond to unexpected situations.
4. Ignoring Individual Training Needs
Every operator has unique strengths and weaknesses, and a one-size-fits-all training approach may not address individual needs effectively. Ignoring these differences can result in some operators being underprepared for specific challenges they might face.
Why It Matters: Personalised training ensures that each operator receives the support they need to excel. Addressing individual learning styles and operational challenges helps maximise the effectiveness of the training programme.
What to Do: Assess the skills and needs of each operator before designing their training plan. Tailor the training to address specific areas where they may need extra support, whether it’s handling particular types of loads or improving spatial awareness.
5. Failing to Evaluate Training Effectiveness
Lastly, many organisations fail to evaluate the effectiveness of their forklift training programmes. Without proper evaluation, it’s challenging to determine whether the training is achieving its intended goals and where improvements may be needed.
Why It Matters: Evaluating training effectiveness helps identify gaps in knowledge or areas where additional training might be required. It also ensures that the training programme remains relevant and effective over time.
What to Do: Implement a system for evaluating the effectiveness of your forklift training programme. This could include regular assessments of operators’ skills, feedback from supervisors, and tracking of safety incidents. Use this information to make necessary adjustments to the training programme.
Conclusion
Avoiding these common forklift training mistakes can significantly enhance both safety and efficiency in your workplace. By ensuring comprehensive initial training, scheduling regular refreshers, emphasising practical experience, addressing individual needs, and evaluating training effectiveness, you can create a more competent and safety-conscious team. Investing in proper forklift training not only complies with legal requirements but also fosters a safer and more productive work environment.
Comments